Insights
Mar 8, 2023 _ insights
Onsite Prefabrication: More than a Process, It’s a Partnership
Prefabrication helps you navigate an uncertain market.
As health systems plan for the future of their facilities, they’re navigating in a time of uncertainty. The problem they face is two-fold:
Ongoing supply chain issues. Material shortages and volatile fuel prices are compounding long-term issues (especially, skilled labor shortages) in a way that exacerbates market instability and increases owner’s risks. While the cost of many building materials leveled out over the end of 2022, that followed the dramatic price increases of the preceding years.
Increased demand for services. This is enough to make anyone involved in construction projects anxious, but health systems face a host of additional pressures. Most notably, an aging population is driving an increased demand for services, and healthcare systems need to take steps now in order to meet those needs. So, despite market uncertainties, many health systems are pushing forward with their projects.
Given this environment, what can healthcare providers do to control costs and mitigate the risk of getting caught in market fluctuations? One answer to consider is Onsite Prefabrication (or Industrialized Construction).
What’s Onsite Prefabrication? And why do it?
Onsite Prefabrication offers an important approach for health systems that are looking to manage this uncertainty. Its advantages include increased speed to market, decreased construction waste, better labor utilization, and lowered costs.
Distinct from traditional prefabrication, which occurs offsite, this approach fabricates building elements within a large, temporary manufacturing facility at the construction site. Imagine a 17,000 SF tent erected onsite where skilled workers work along an assembly line to produce large components of the building: exterior wall assemblies, interior wall assemblies, mechanical system assemblies, and so on. Working conditions are more predictable, ensuring increased safety, quality, and efficiency. This also makes the coordination of skilled trades much easier.
When they roll off the assembly line, these pieces—which can be as large as 13’ x 30’ (much larger than can be transported from offsite)—are hoisted into place by a crane. You can imagine the time saved.
The proof is in the pudding.
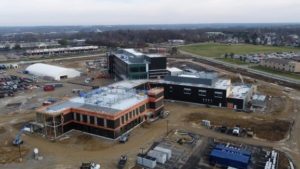
GBBN is currently partnering with Bon Secours Mercy Health and Danis Construction on a project that is using this approach, and the results are impressive. At Mercy Health Kings Mills Hospital in the Cincinnati area, we’re seeing:
- An 81% improvement in labor utilization rates
- A 51% reduction in days onsite
- Zero safety incidents
When all is said and done, we anticipate that our partnership with Danis and Bon Secours Mercy Health will help shave up to five months off the construction schedule. That’s a lot of savings in terms of labor and construction costs. It also means the building will be online, helping patients, and generating revenue sooner.
So, how do you know if this approach is right for you?
When and who? Trusted partners help you through uncertain times.
There are some obvious constraints about when onsite prefabrication is appropriate. The scale of a project and the size of the site are key factors. Given the upfront cost in transporting the machinery and erecting the temporary structure, the project needs to be of a certain scale in order to recoup those costs. The site itself can also pose a difficulty. Even if the project is appropriately scaled, it might not be a prime candidate if the site doesn’t have room to accommodate the structure.
Most importantly, our experience at Bon Secours Mercy Health Kings Mills Hospital has shown the value of finding the right partners.
In order to take advantage of the speed and efficiency that onsite prefabrication offers, a more integrated design approach is essential. The client, architect, engineer, and construction team all need to work together early to set goals and make design decisions. Many design decisions that are typically refined through the construction submittal process—often, while skilled workers are onsite, waiting for feedback—are made up front. It’s a more integrated design/construction team making these decisions, operating with a much more tightly defined set of technical and logistical constraints. For example, it takes close collaboration to maximize the efficiency in exterior wall assembly panels before the fabrication process begins. Of course, this collaboration continues throughout construction, but many of the decisions are more front-loaded than usual.
A good working relationship, based on mutual respect, trust, and understanding, helps the team find the right solutions. Our long-standing relationship with Bon Secours Mercy Health, who we have developed a system of prototypes for, and our mutual trust and respect with Danis Construction, is helping us control costs and deliver a quality project in a challenging market.
Mickey LeRoy, AIA, ACHA, LEED AP is a principal at GBBN. He leads teams in all phases of planning, design, and delivery of multi-faceted healthcare projects, like TriHealth’s Thomas Center. He works closely with leading healthcare systems, like Bon Secours Mercy Health, to develop efficient clinical prototypes that can work with different building scales. With previous experience in public relations and marketing, Mickey’s communication skills complement his abilities in design and project management.
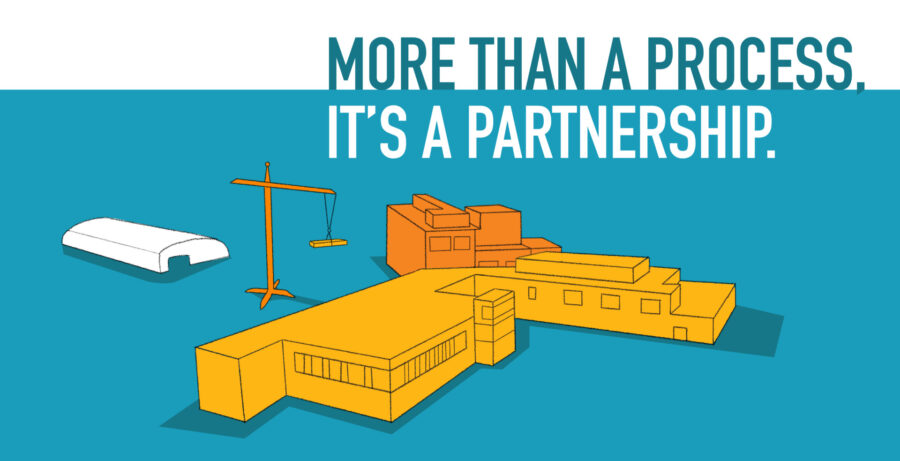